Key Takeaways
- Cement brick making machines automate brick production, boosting efficiency and ensuring consistent quality for small to large-scale construction projects.
- These machines reduce manual labor, cut production costs, and offer versatile output options—including hollow, solid, and paver bricks—to meet diverse construction needs.
- Advanced features like full automation, adjustable molds, and robust build quality enhance productivity, minimize errors, and ensure long-lasting equipment performance.
- Choosing the right machine depends on production volume, automation level, project specifications, and budget to optimize return on investment.
- Regular maintenance and proper operation are essential for maximizing machine lifespan, minimizing downtime, and sustaining high-quality brick output.
Cement brick making machines automate brick production using hydraulic or mechanical pressure to mould raw materials into uniform bricks. These machines significantly reduce manual labour whilst ensuring consistent quality across small to large-scale construction projects. Production capacities range from 5,000 to 30,000 bricks per eight-hour shift, with models available from manual to fully automatic systems. Leading suppliers like Block Machine Lontto provide versatile solutions for diverse construction requirements.
What Is a Cement Brick Making Machine?
A cement brick making machine automates the process of producing cement-based bricks using a mix of cement, sand, water, and aggregates. These machines use hydraulic or mechanical pressure to mold raw material into uniform bricks, reducing human effort and maintaining consistent quality. Factories and construction sites in high-demand regions, such as Chicago, deploy these machines to increase output and lower costs.
Lontto, with operations in Chicago, supplies cement brick making machines fitted for small, medium, and large-scale brick production. Their machines offer automated mixing, molding, and stacking functions, helping businesses achieve faster turnaround times. Production capacities range from 5,000 to 30,000 bricks every 8 hours, covering manual and fully automatic lines.
Most models operate with power ratings between 7.5 kW and 45 kW and feature adjustable molds to accommodate different brick shapes. Lontto‘s equipment solutions address key concerns for contractors and manufacturers, such as labor reduction, limited site space, and stringent quality requirements in construction projects. These machines support both hollow and solid brick output, meeting regulatory and structural standards in concrete construction.
Key Features to Look For
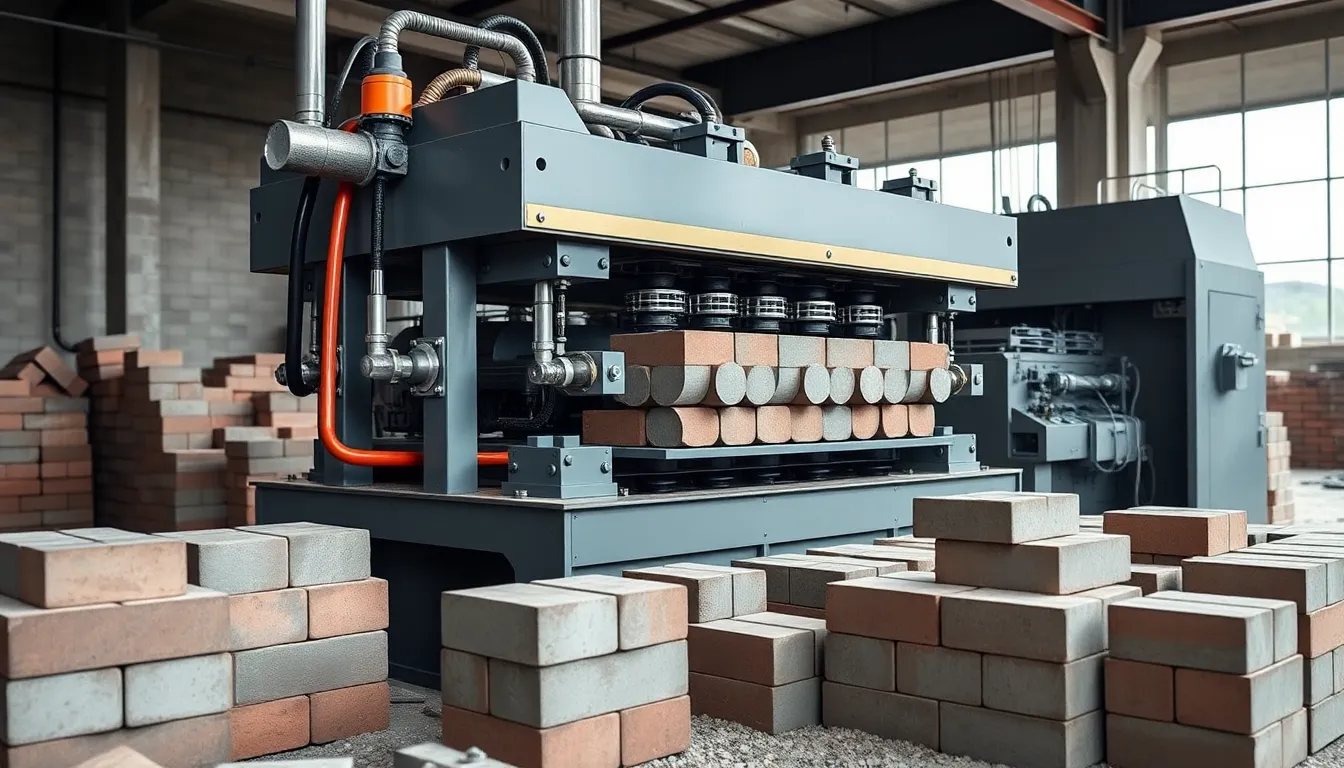
A cement brick making machine includes specialized features that impact production efficiency, product quality, and equipment longevity. Construction businesses in Chicago, including those sourcing from Lontto, often prioritize automation, output, and durability.
Automation and Technology
Automation accelerates brick production and minimizes human error. Machines include manual, semi-automatic, and fully automatic models. Semi-automatic units use hydraulic systems that improve density and uniformity. Fully automatic machines integrate PLC controls, streamlining the process with computer-regulated pressure, vibration, and timing. These systems consistently produce high-quality bricks—up to 4,000 per shift—while reducing labor. Lontto’s advanced models support flexible manufacturing, producing hollow, solid, and paver blocks with energy-efficient drives that help lower operational costs.
Production Capacity
Production capacity directly affects project timelines. Manual machines output fewer than 1,000 bricks daily, suitable for small projects. Semi-automatic models typically create 500 to 1,000 blocks per hour, ideal for medium-scale work. High-end hydraulic automatic machines, such as Lontto’s QT6-15, deliver over 20,000 bricks per 10-hour shift with molding cycles lasting just 10–15 seconds. Adjustable molds allow businesses to meet precise specifications for both hollow and solid bricks, addressing regulatory and structural requirements in demanding construction zones like Chicago.
Durability and Build Quality
Durability determines equipment lifespan and maintenance needs. High-grade materials, including reinforced steel, protect machines from excessive wear under intensive hydraulic pressure—usually around 15–20 MPa. Lontto machines offer robust structures that stand up to continuous use in industrial settings. Well-engineered designs contribute to low maintenance intervals and stable operation, which helps prevent downtime and cost overruns in large-scale building projects. Consistent pressure and solid construction ensure reliable brick compaction and uniform product quality.
Pros and Cons of Cement Brick Making Machines
Cement brick making machines streamline brick manufacturing for contractors and construction businesses. Lontto in Chicago supplies models with automation and flexibility for small to large projects.
Benefits for Businesses
Cement brick making machines raise productivity by automating processes, cutting manual labor needs by up to 75%. High production rates—up to 4,000 bricks per eight-hour shift—help businesses complete projects faster. Consistent quality outputs support regulatory compliance, critical in Chicago’s strict construction market. On-site production with Lontto machines reduces transportation costs and supplier delays, supporting cost control. Machines support multiple brick types—such as interlocking or hollow—through mold changes, letting businesses switch between products for different construction demands. Efficient raw material usage, supported by Lontto’s automated mixing, reduces waste and boosts profitability.
Potential Drawbacks
Cement brick making machines involve notable initial investment, especially for fully automatic models, which may challenge smaller operations. Lontto’s high-capacity systems suit larger Chicago projects but might not fit smaller-scale budgets. Skilled operation remains necessary for optimal performance; improper use can lower brick quality and shorten machine lifespan. Cement-based brick production contributes more CO2 emissions compared to alternatives, raising environmental concerns and compliance requirements. Some machines specialize in specific brick forms, so switching to other types may require additional molds or equipment. Ongoing maintenance and adherence to operating guidelines are essential to maintain reliability and consistent output over time.
Top Models of Cement Brick Making Machines in 2024
Leading cement brick making machines in 2024 include updated manual, semi-automatic, and fully automatic units optimized for small to industrial-scale projects. These models address labor output, automation, and space efficiency needed by Chicago-area construction firms.
Entry-Level Options
Entry-level cement brick making machines in 2024 improve startup and small-site production with cost control and flexibility. LONTTO’s LMT4-35 produces 2,880 hollow blocks every 8 hours, runs on 7 kW, and supports frequent startups with durable construction and simple controls. The LMT4-26 offers semi-automatic operation with 3,200 blocks per shift using just 6 kW, and batch cycles lasting 20–26 seconds. For mobile setups, the LONTTO QMJ4-45 delivers 2,400 bricks per 8-hour shift, while the QMY4-30 produces up to 5,800 blocks, suited for smaller crews in space-limited areas. Chicago users selecting these models meet most local building demands with minimal manpower.
Industrial-Grade Machines
Industrial-grade cement brick making machines meet high-volume demands and consistency for large projects in Chicago. Fully automatic models like VessMachine processes 10,000–18,000 hollow blocks daily, driven by robust 54 kW systems and advanced hydraulic motors producing up to 42,500 kg vibration force. The 2024 popular hollow brick machine on Made-in-China suits factories producing over 15,000 bricks in 8 hours, listed at $115,000–$138,000 per unit. Bess brick making machines supply both semi-automatic and automatic solutions with factory-level outputs, robust aftersales service, and full equipment sets ranging from $65,700 to $89,980. These systems produce consistent blocks, reduce operator error, and fit continuous multi-shift operations common among Chicago manufacturers.
How to Choose the Right Cement Brick Making Machine
Selecting the right cement brick making machine depends on aligning machine features with project goals. Factors like output, automation, and budget directly impact efficiency for Chicago construction businesses.
Assessing Your Production Needs
Evaluating production needs focuses the search for an efficient cement brick making machine. Output requirements shape the choice—manual and semi-automatic units from Lontto in Chicago suit small projects needing up to 5,000 bricks per day, while fully automatic models like Lontto’s QMY12A and QT8-15 reach 34,560 and 120,960 blocks per 8-hour shift respectively. Product type matters, as certain machines offer interchangeable molds for solid, hollow, or paving bricks to support local regulatory standards. Automation reduces labor costs and increases speed but warrants an upskilled operator. Project scope and brick specifications drive model selection, with hydraulic multifunctional systems preferred for high-volume or mixed product demands.
Budget Considerations
Determining budget for a cement brick making machine includes calculating upfront investment and long-term costs. Manual machines cost less to purchase, starting around $2,800, but require more labor and offer lower efficiency. Automated models, such as Lontto’s QT8-15, reach higher prices but decrease ongoing labor expenses by implementing advanced controls and hydraulic systems. Site preparation, power installation, and storage sizing raise initial costs for high-capacity plants in Chicago, often exceeding 100–300 square meters for layout. Operational spending extends to maintenance and energy; machines equipped with efficient drives and computerized controls from Lontto reduce power bills and downtime over the machine’s service life. Quantifying these elements ensures budget alignment with business targets.
Maintenance and Operating Tips
Cement brick making machines require structured maintenance and methodical operating routines to keep output consistent and extend machine life. Lontto‘s Chicago customers apply these procedures to maximize equipment value and production efficiency.
- Pre-Operation Checks: Operators inspect all areas for debris, confirm fasteners are secure, and verify control systems function. These checks stop foreign matter from entering conveyors or hydraulic presses during high-volume work cycles.
- Routine Cleaning: Staff wash machines after every use, focusing on cement residue around mold cavities and pressure heads. Cleaning with water and proper tools reduces corrosion, ensuring long-term performance in Lontto’s semi-automatic and fully automatic units.
- Lubrication: Teams lubricate moving joints and mechanical assemblies, but avoid excessive application. They focus on high-friction locations, preventing premature wear across shift-intensive schedules.
- Periodic Maintenance: Managers schedule inspections and part replacements based on production metrics, such as cycle counts or elapsed time. Scheduled maintenance covers belt calibration, damage detection, and hydraulic fluid verification on Chicago job sites.
- Operational Awareness: Supervisors halt machines immediately if unusual noises or faults occur. Resolving these incidents before resuming operation prevents larger equipment failures.
- Tightening Loose Components: Technicians routinely tighten bolts and connectors to counteract loosening from vibration during continuous brick production, reinforcing Lontto’s reliability standards.
Lontto in Chicago structures after-sales services to support adherence to these procedures, reducing plant downtime and supporting consistent hollow and solid brick output for commercial projects.
About Lontto
Lontto, located in Chicago, IL, is a leading manufacturer specialising in block and brick making machines.
Under the leadership of CEO Chao Zhang, Lontto offers a wide range of products, including concrete block machines, mobile block making machines, and compressed earth block machines. The company also provides services such as installation and training to ensure the efficient operation of their equipment, helping clients achieve high-quality production with ease.
Contact:
Chao Zhang, CEO
Phone: 708 260 8300
Email: [email protected]
Website: www.block-machine.net
Location:
4992 S Austin Ave, Chicago, IL 60638, USA
Frequently Asked Questions
What is a cement brick making machine?
A cement brick making machine automates the process of producing bricks by molding a mixture of cement, sand, water, and aggregates into uniform shapes. It ensures consistency, increases productivity, and reduces manual labor in construction projects.
How does a cement brick making machine benefit construction projects?
These machines speed up brick production, maintain strict quality standards, and significantly reduce labor costs. They enable companies to meet tight deadlines and comply with regulatory requirements, especially in demanding markets like Chicago.
What types of cement brick making machines are available?
There are manual, semi-automatic, and fully automatic cement brick making machines. Manual machines suit smaller projects, while semi-automatic and fully automatic models are ideal for higher-volume or industrial-scale projects.
What key features should I look for in a cement brick making machine?
Important features include automation level, production capacity, mold flexibility for different brick sizes, energy efficiency, and robust construction for durability and low maintenance.
How do I choose the right machine for my needs?
Assess your project’s scale, required output, available space, and budget. For smaller projects, a manual or semi-automatic machine may suffice, while larger sites benefit from fully automatic models with higher production rates.
What is the typical production capacity of these machines?
Depending on the model, cement brick making machines can produce anywhere from 5,000 to over 30,000 bricks per 8-10 hour shift.
Are there any drawbacks to using cement brick making machines?
Drawbacks include higher upfront costs for advanced automation, need for skilled operators, regular maintenance requirements, and environmental concerns associated with cement production.
How much power do cement brick making machines require?
Power ratings vary from around 7.5 kW for small machines to 45 kW or more for large, fully automatic units. The power requirement depends on the size and automation level of the machine.
How important is regular maintenance for these machines?
Regular maintenance is vital. It ensures consistent performance, prevents costly breakdowns, and extends the machine’s lifespan. Recommended routines include pre-operation checks, cleaning, lubrication, and tightening parts.
What after-sales support is available for these machines in Chicago?
Suppliers like Lontto offer comprehensive after-sales services in Chicago, including parts supply, technical support, machine installation, and operator training to ensure smooth operation and minimal downtime.